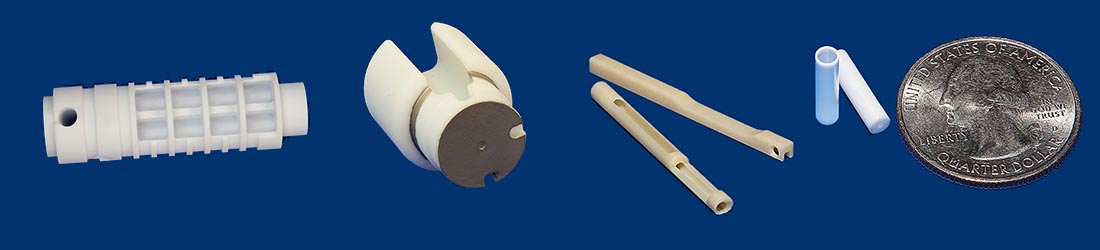
Ceramic Materials & Capabilities
Capabilities | Finished | Standard |
---|---|---|
Flatness (as ground) | .0001″/” | .001″/” |
Flatness (mechanical polish) | .000002″ | —— |
Straightness | .0002”/” | .001”/’ |
Circularity | .0001”/” | .001”/’ |
Cylindricity | .0001”/” | .001”/’ |
Perpendicularity | .0001”/” | .001”/’ |
Squareness | 0:00.30o | 0:30.00o |
Angularity | 0:00.30o | 0:30.00o |
Parallelism | .00005”/” | .0005”/” |
Surface Roughness (as ground) | —— | 32u” |
Surface Roughness (manual polish) | 8u” | —— |
Surface Roughness (mechanical polish) | >2u” | —— |
Manufacturing Materials
Alumina-based ceramics are without a doubt the largest selection of progressive ceramics machined by ICPI. Aluminium Oxide (or Alumina), Al2O3, is a leading engineering material. It provides a blend of excellent electrical and mechanical properties, providing the means for a broad spectrum of functions.
Alumina can be manufactured in an array of purities with additives intended to improve its properties. A multitude of ceramic processing procedures can be implemented, including net shape forming or machining to yield a large selection of shapes and sizes of components. Additionally, it can be easily connected to other ceramics or metals by the use of metallization and brazing methods.
An extensive understanding of the vital blend of these properties is a must, which is why ICPI has earnestly studied the traits and behavior of our Alumina products to give you the most supreme component for your specific application.
The precise appeal of Aluminium Nitride is its effective electrical insulation coupled with its tremendous thermal conductivity. Its applications are primarily in electronics where heat removal is necessary.
It can be generated by sinter and dry press, or by hot pressing with applicable sintering treatments.
NOTE: The material suffers surface oxidation above 700°C.
Barium titanate is a ferroelectric ceramic material, with piezoelectric properties and a photorefractive effect. It can exist as a white powder, be transparent as larger crystals, or remain in five phases of solid form, listing from high temperature to low temperature: hexagonal, cubic, tetragonal, orthorhombic, and rhombohedral crystal structures.
Produced by heating titanium dioxide and barium carbonate, there is a progressive reaction through liquid phase sintering.
Barium titanate experiences two-phase conversions that alter the volume and crystal shape. This phase alteration produces composites in which the barium titanates possesses a negative bulk modulus (Young’s modulus), signifying that when an energy responds to the additions, there is then a shifting in a different course, additionally hardening the fusion.
NOTE: As is in numerous oxides, barium titanate is insoluble in water but attacked by sulfuric acid.
Boron Nitride (BN) is a non-toxic and non-porous, white solid material. Extremely anisotropic in its mechanical and electrical properties, BN is highly protected from thermal shock. It also has tremendous thermal conductivity, in addition to being an excellent electrical insulator. While it can be produced by pressing/sintering techniques, the purity-rich pyrolytic material is created by a vapor deposition process.
NOTE: This material is stable in reducing and inert atmospheres up to 2800°C, and in oxidizing atmospheres to 850°C.
Fused Silica was primarily implemented in the flat glass industry as rollers in glass tempering furnaces, mainly in the form of solid rollers, but additionally as hollow rollers.
Fused Silica is comparable to quartz glass because it possesses a purity-rich powder and fine pore structure, but in actuality it’s quartz glass that is sintered, producing an extremely low expansion coefficient, and therefore an expectionally invaluable thermal shock resistance. The creation of this material provides a special use for ignition crucibles and dishes, firing supports, and castables of other geometries.
CAUTION: Due to its physical structure this material should not be utilized at temperatures greater than 1000°C.
MACOR(R) is the trade name for a Machineable Glass Ceramic. Designed for the use of conventional tools for its machining, it is the experience and tooling at ICPI that makes a tremendous difference in making parts with this material, otherwise cracking and chipping could cause high yield losses. The material has zero porosity, non-wetting, and won’t deform like other ductile materials. It’s a superior insulator at elevated temperatures, extreme voltages and varied frequencies, and it won’t outgas in vacuum environments. When appropriately baked out, its coefficient of thermal expansion easily parallels most sealing glasses and metals. NOTE: This material has temperature limitations; deforming could occur at and above 850 degrees C.
Manganese zinc is a ferrite formed by reacting metal oxides and magnetic oxides to form polycrystalline magnetic oxides. This oxide has a much lower conductivity than metals, allowing microwave signals to pass through them. Depending on their magnetic behavior, materials can be classified as diamagnetic, paramagnetic, ferromagnetic, anti-ferromagnetic, and ferromagnetic. Choosing a ferrite solution depends on the specific characteristics you are looking for, including EMI source, frequency of desired signal versus noise, circuit impedance and environmental conditions. ICPI has extensive expertise in fabricating small and intricate shapes.
Nickel zinc is a ferrite formed by reacting metal oxides and magnetic oxides to form polycrystalline magnetic oxides. This oxide has a much lower conductivity than metals, which allows microwave signals to pass through them. Depending on their magnetic behavior, the materials can be classified as diamagnetic, paramagnetic, ferromagnetic, anti-ferromagnetic, and ferromagnetic. Choosing a ferrite solution depends on the characteristics you are looking for, including an EMI source, frequency of desired signal versus noise, circuit impedance, and environmental conditions. ICPI has extensive expertise in fabricating small and intricate shapes.
As a high purity grade of Silicon Di-Oxide material, quartz is resistant to most chemicals, which makes it a choice material in semiconductor fabrication. Quartz components are typically at a relatively lower-cost when compared to other ceramic materials due to less machining time required. Surface finishes can be ground, etched and polished. Quartz may also be used for its piezoelectric properties.
Unlike a multi-crystal oxide formation, Sapphire is the single crystal form of Aluminum Oxide and is typically used for its durability as a window in optical systems. Several characteristics in its fabrication can be determined by the design requirements such as crystal orientation, ground or polished surfaces, and material grade in relation to UV light. Sapphire also has excellent chemical resistance and hardness. Custom sapphire components made at ICPI can be tailored to meet your specific application needs.
ICPI’s engineers are consistently accessible to provide you with the most appropriate recommendations in regards to the strengths and weaknesses of each ceramic material for your specific needs. Silicon Carbide, for instance, is produced in two ways: Sintering and Reaction Bonding. And each manufacturing technique significantly influences the outcome of the microstructure.
Reaction bonded SiC is produced by permeating compacts, consisting of combinations of SiC and Carbon, with liquid Silicon. The Silicon reacts with the Carbon producing more SiC which joins the initial SiC particles.
Sintered SiC is created from pure SiC powder with non-oxide sintering aids. Standard ceramic forming methods are implemented and the material is sintered in an inactive atmosphere at temperatures that reach or exceed 2000°C.
Both forms of Silicon Carbide (SiC) are highly safeguarded from wear with superb mechanical properties, which include thermal shock resistance and high temperature stability.
Silicon Nitride is created in two fundamental ways; Reaction Bonded Silicon Nitride (RBSN), Hot Pressed Silicon Nitride (HPSN) and Sintered Silicon Nitride (SSN).
RBSN is produced by directly reacting the compacted Silicon powder with Nitrogen, and generating a low-density product in contrast to the Hot Pressed and Sintered Silicon Nitride; although this method has a limiting volume alteration, permitting net shape forming. Additionally, the HPSN and SSN material is comprised of sintering aids and it yields preferred physical properties that are applicable for more challenging purposes.
Additionally, Silicon Nitride’s low thermal expansion coefficient provides excellent thermal shock resistance in comparison with the majority of ceramic materials and it exhibits superb temperature stamina, creep and oxidation resistance.
In its purest form, changes in the structure of crystal hinder any mechanical functions. However, Zirconia, when it’s stable, is created by the inclusion of Calcium, Magnesium or Ytrium Oxides, and can produce extremely elevated firmness, stamina, and significant rigidity.
Zirconia (TZP) supplies corrosion and chemical resistance to temperatures that highly exceed the melting point of Alumina. Utilizations in oxygen sensors and high temperature fuel cells are actualized as a result of Zirconia possessing moderate thermal conductivity and being an ionic conductor greater than 600°C.